It’s a question as old as the heating designs themselves— Which is superior, water tube or fire tube boilers? While both technologies have developed enormously throughout their lifetime, both water tube and fire tube designs possess certain inherent benefits and shortcomings. In this blog, we will highlight what makes these two boiler styles unique, putting a magnifying glass to the advantages and disadvantages of each design.
WATER TUBE
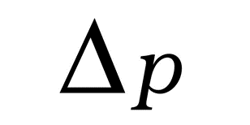
WATER TUBE ADVANTAGES
With the water tube design, these boilers typically feature a quicker startup and response time to changing conditions with no major standby losses. With less water passing through the heat exchanger at any given time, the overall footprint of a water tube model can be significantly less than that of a fire tube model and it allows for wider capabilities in the output ranges. The central burners found in these models typically allow higher temperature outputs and differentials for more demanding process loads. The higher temperatures come with the inclusion of higher pressures, which can be passed through the water tube units to the typical design.
WATER TUBE DISADVANTAGES
Overall, with the water tube design, the concern of fouling is heightened. Water treatment of this boiler style must be watched carefully, as it is important for the efficient operation of the unit and prevention of scale. Though this is not something specific to water tube design, scale build-up in a water tube model can progress at a faster rate because of the lower water mass and frequency of passes. The water tube design requires continuous flow during its operation, so hot spots in the heat exchanger do not decrease the life of the unit. Their minimum flow rates are typically higher in a water tube design to compensate for the reduction in water volume. The smaller volume of water in the water tube could result in the inability to instantaneously accommodate large peaks in hot water demand. This can be remedied, however, with the inclusion of an external storage tank.
FIRE TUBE
As you could most likely guess, the design of the fire tube boiler is an inverted water tube design. The fire tube blueprint features water in the main shell of the unit and the tubes house the heated gas vapors. Similarly, fire tube boiler tubes vary in size, depending on the capacity and style.
FIRE TUBE ADVANTAGES
The water volume of a fire tube model is 4-8 times that of a water tube design. This makes it optimal in scenarios where there are high peaks in demand once or twice a day and relatively no demand for the remainder of the day. Due to the number of tubes present, it is easier to maintain hot water demand even if one tube has failed. With this design, the effects of poor water quality may take longer to manifest and develop performance issues.
FIRE TUBE DISADVANTAGES
The larger volume of water comes with a larger footprint, which can make it difficult to place in some applications. This large water capacity and lower flow rates, which are typically less efficient to transfer heat, make it harder to adapt to rapid temperature change. Since it takes longer to heat the large volume of water, this also can mean that startup times are increased. The overall capability of a fire tube boiler is measured at peak demand. This can have negative effects if the application calls for constant water flows at these peak conditions, since it would be unable to accommodate this consistently. Additionally, standby losses are generally greater with the fire tube design, due to a large amount of water in the heat exchanger.
WHEN IT ALL BOILS DOWN...
Water tube and fire tube designs have been pitted against each other since the establishment of different heating methods. However, in today’s market, the historical lines for each type of equipment have become increasingly blurred. Water tube designs, like our P-K STORM®, have incorporated manifolds, to not only pass water through one or two tubes at a time, but five to ten simultaneously. This increases the flow capabilities, pressure drop limitations, as well as heat exchange deficiencies that have burdened this exchanger style. Fire tube designs have begun to decrease their overall water volume, to accommodate for wider ranges of heating and turndown capabilities. This has also meant that some of the disadvantages of water tube designs can be found in some forms of fire tube models, depending on how the heat exchanger is applied.
For more information on our ever-expanding product offering, please visit our website at www.PattersonKelley.com, or contact your nearest Patterson-Kelley representative.